L A S I T A
OPTIONS
GLAZING
Good glazing is an essential part of any good window or door. In addition to excellent energy-saving characteristics quality glass units nowadays have, they offer many possibilities for comfort and protection. In our Skyline system, sliding doors and glass walls starting from the ground have tempered safety glazing as standard both on the inside and outside. It is possible to choose solar protection glass to keep away the hot summer sun, sound reduction glass for extra comfort and maintaining a quiet setting, as well as many other special options upon request. A well-thought-through glazing package ensures comfortable living for many years, can be an integral part of a cost-efficient sustainable household and much more.
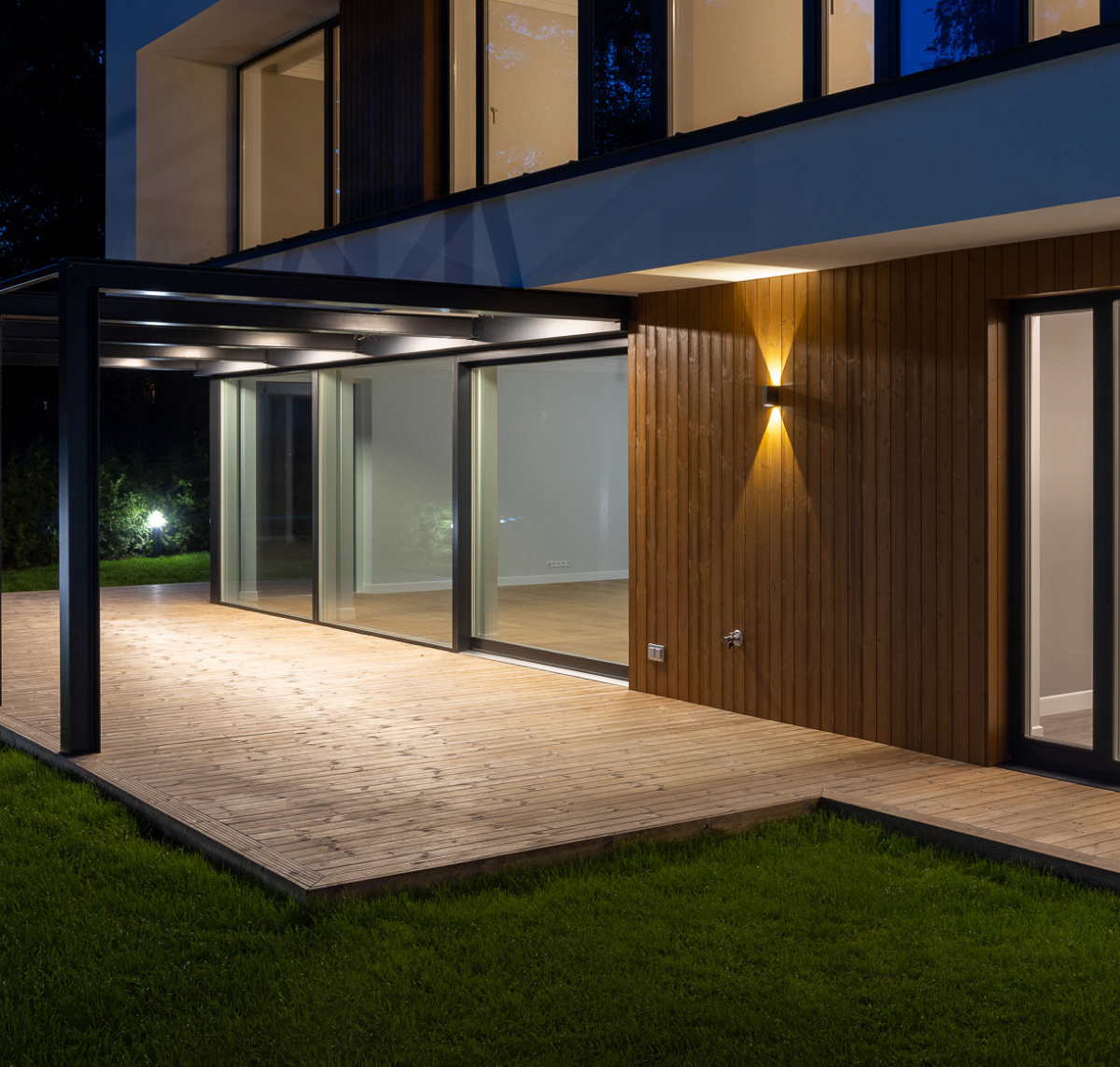
STANDARD GLAZING
Triple glazed insulated glazing with two selective glass types are used. As standard, the inward and outward glass are equipped with selective characteristics (Energy Saver) and the middle glass is float. In the Skyline system, when the products are starting from the floor, the standard glazing already includes heat-treated toughened tempering both on the inside and outside for extra safety. Depending on the specific Skyline type, the products have a standard glass U value of Ug=0,5-0,6 W/m2K. As standard, the casements between the glass layers are filled at least 90% with argon gas. Warm edge, composite spacers are used in between the glass for extra isolation and to avoid the risk of condensation. The standard color options for spacers are light grey, white and black.
Tempered glass is 4-5 times stronger than standard float glass, providing resistance to various unwanted hazards as well as being thermally more resistant. Historically, tempered glass is used in cases where there is a risk that someone or something can accidentally fall into the glass. If this were to happen, a tempered glass is strong and less likely to break. When tempered glass does break, however, it breaks into small blunt pieces not posing a threat to one’s safety. One needs to be aware that tempered glass does not prevent a person from falling through the window or door when it breaks, which is why tempered glass is usually used on ground floors where there is no risk of falling. Because of its strong characteristics, tempered glass is practically helpful also on the outer surface where a risk of baseball hits, rocks from underneath the lawn mower, etc. could harm or even break the glass otherwise. Tempered glass varies in thickness according to the size of the Skyline system product, but in standard cases glass of 4mm or 6mm is used.
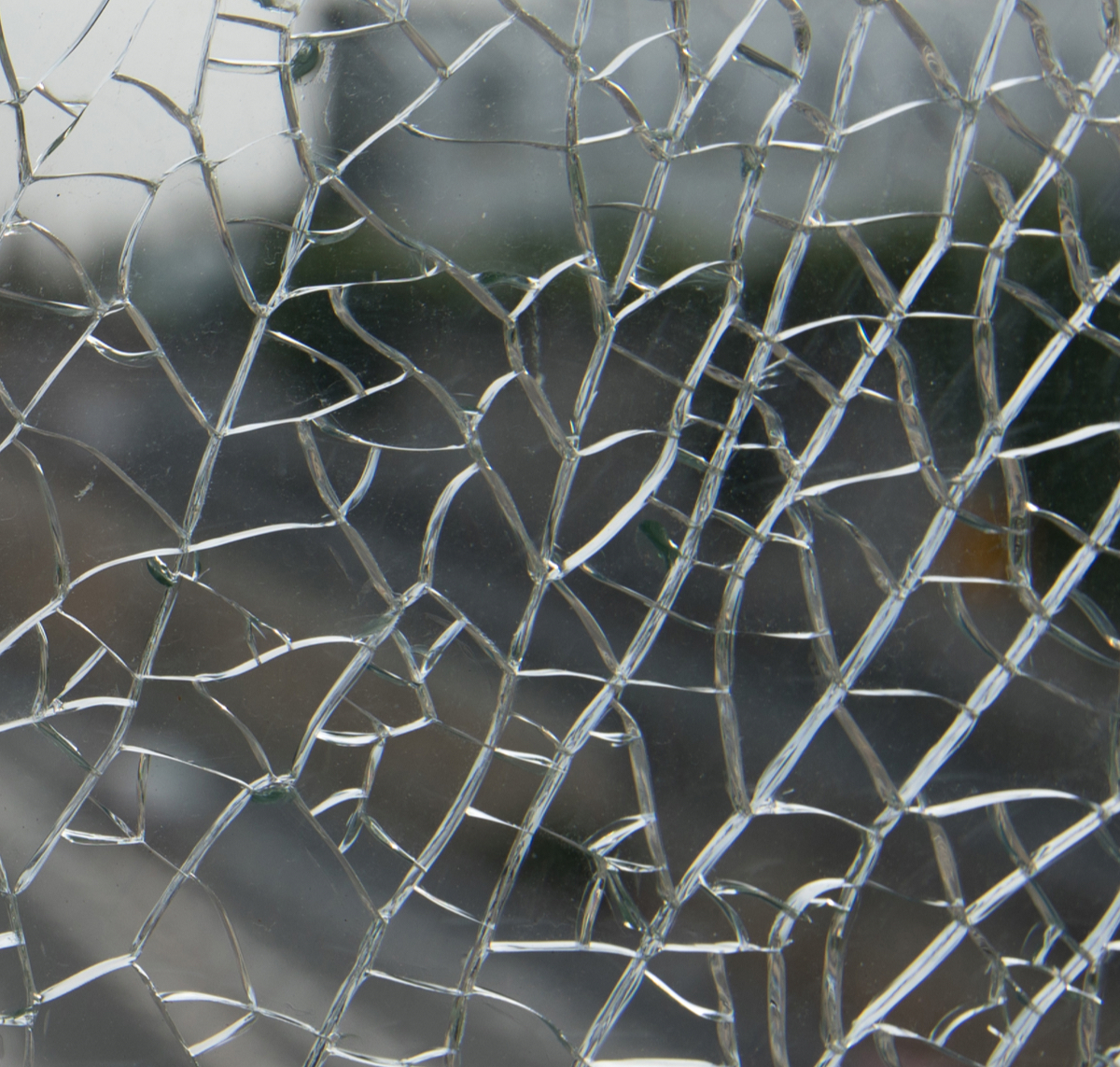
SAFETY AGAINST FALLING
In cases where there is a danger of falling when the glass is broken, laminated glass is mandatory. Laminated glass consists of two glass layers, which are held in place by an interlayer (PVB). The interlayer keeps the layers of glass bounded even when broken and thus prevents the danger of injuries and keeps a person from falling through the glass when it is broken. Lasita ́s sales staff implements laminated glass in cases of falling risk as standard procedure, however from drawings information may be insufficient. Because of this, it is best when one points out these cases for the optimal end-result.
SOUND REDUCTION
As standard, the Skyline system has a sound reduction value of Rw=33dB and Rw+Ctr=30dB. Because of market demand and our constant need to develop further, we have developed and tested a sound reduction product that reaches values of Rw=46dB and Rw+Ctr=42dB. We are very proud that based on the 3dB rule, we have managed to reduce the noise to the human ear many times over. As the standard Skyline product consists of a triple glazed 3K (stands for triple glazing), the highest tested option of Rw 46dB consists of 3K 66.1Sil+4+44.1Sil, hence using silencing laminates both on the internal and external surface. Because such great values are usually not needed in residential homes, we have also developed products for the midlevel.
SPECIAL GLASSES
Upon request, it is possible to add many types of special characteristics to your Skyline system. Some of these more commonly used glass options are decorative glass in Satin and Crepi that are available where privacy is desired. These types of glass let the light come into the room but are not transparent. It is also possible to add security features to your home by using security glass in your Skyline system. The function of this glass is protection from external active intrusion (vandalism, burglary, firearm attacks). Laminated security glass consists of two or more glass layers, which are held in place by an interlayer (PVB).
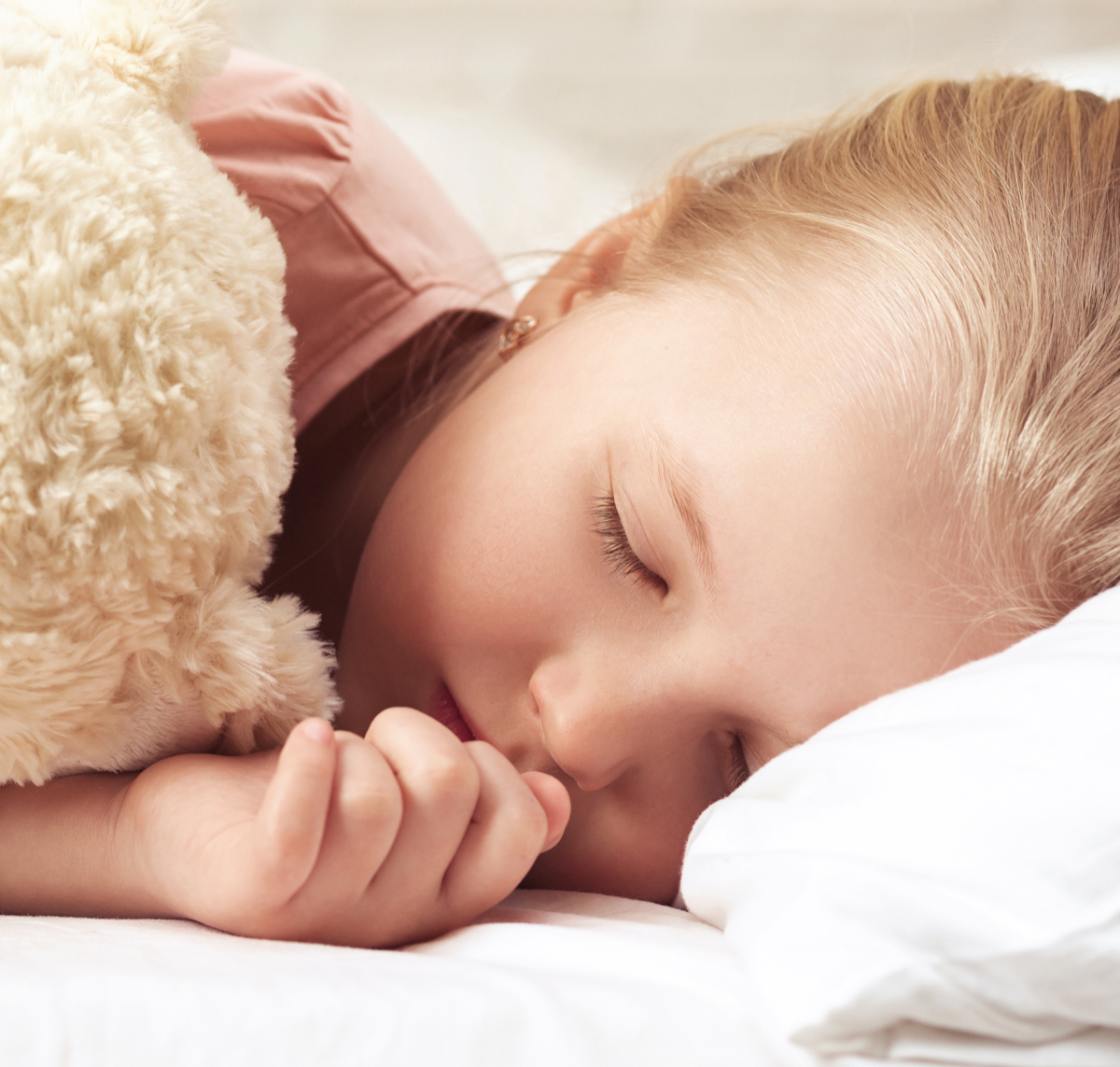
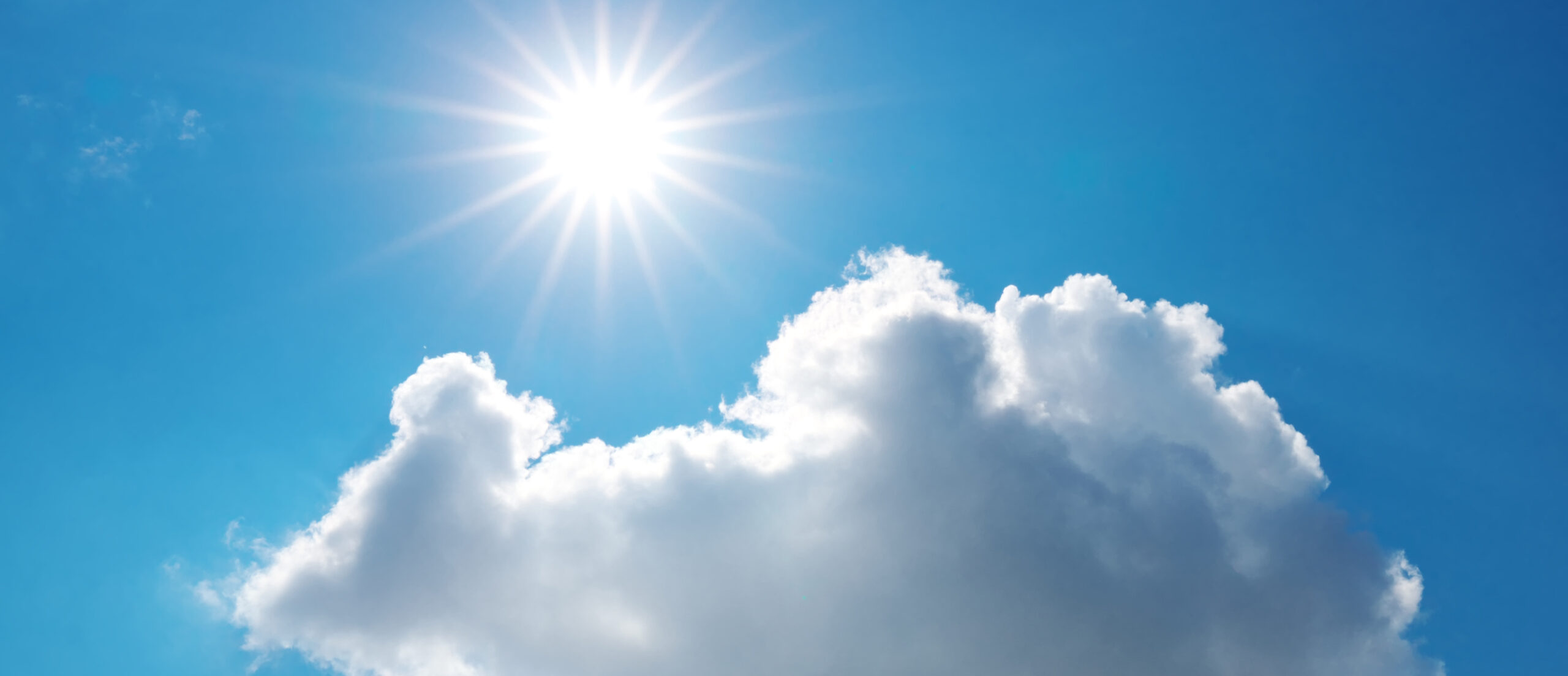
SOLAR PROTECTION
Solar heat and light energy reaching the glass is partially reflected back, partially absorbed in the glass and partially transmitted through the glass. Solar protection glass reduces solar energy coming through the glass, reflecting most of it back rather than letting it indoors, thus preventing the rooms from overheating in case of heavy sunlight. Combination glass options, in which solar control function is also combined with energy saving function, are used by Lasita. This provides maximum user comfort as the glazing works as protection against sun, but still has great U-value to keep the warmth indoors in winter months. Normally, sun protection glass is the outmost glass in the glazing and replaces the regular energy-saving, selective glass.
Solar control function can also be combined with other functions of the glass: safety, sound insulation, etc. It is important to keep in mind that the more solar protection needed, the less natural light will be transmitted into the room. Although great solar protection glass reaches a g-value of under 19%, or as commonly presented g=0,19, the light transmitted into the room will be less than 45%. This is why, as standard, we recommend in the Nordic countries a mild sun protection glass, which in triple glazing has a g value of 35% or g=0,35, but still lets ample light into the room (SP Mild). Cases where more sun protection is needed may be, for example, south facing faćades of houses in open spaces and fields. In this case a g value of g=0,32 is usually sufficient in Northern Europe and a SP Medium glass is used. In extreme cases where there is a lot of sunlight that needs to be absorbed by the glass, a triple glass reaching g=0,28 is used (SP Strong).
The three standard sun protection options in Lasita systems are as follows:
g=0,35 (SP Mild)
g=0,32 (SP Medium)
g=0,28 (SP Strong)
If needed, even milder or stronger sun protection glass is available upon request. Contact Lasita ́s sales staff for inquiries.